Technology A - M
From Bearded Needle to Mock Seams.
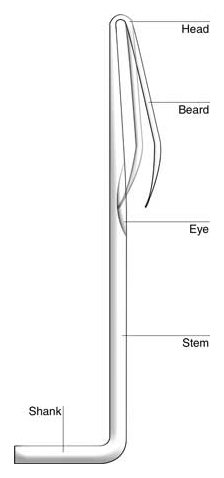
Bearded Needle
The bearded needle was used by William Lee in his stocking frame to enable a single needle to undertake the tasks achieved by handknitters with two needles. The needle consists of five main parts.
- Shaft or stem – used with the jack sinkers to form new loops.
- Head – the point at which the stem is bent to form the beard.
- Beard – the needle continues from the head to be turned back on itself to form the beard. The beard is used to trap new loops while old loops are pushed over the top.
- Groove – a small groove is worked into the stem of the needle to allow the beard to fit flush with the stem and ensure the old course is pushed over the beard.
- Shank – The shank is used to attach the needle to the frame. Lee placed the shank into molten lead held in a mould. Once cooled and removed fro the mould, the lead held the needle in the frame. For fine gauge frames, two or three needles were cast together in the same piece of lead.
A bearded needle shown with the beard in the open and closed positions. The needle consists of five main parts. 1. Shaft or stem – used with the jack sinkers to form new loops. 2. Head – the point at which the stem is bent to form the beard. 3. Beard – the needle continues from the head to be turned back on itself to form the beard. The beard is used to trap new loops while old loops are pushed over the top. 4. Groove – a small groove is worked into the stem of the needle to allow the beard to fit flush with the stem and ensure the old course is pushed over the beard. 5. Shank – The shank is used to attach the needle to the frame.
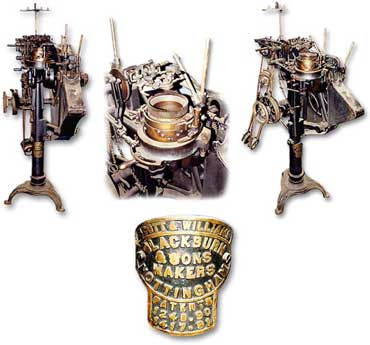
Circular Knitting Machines
As the name suggests, circular machines contain a circular needle bed. Machines are manufactured in a range of diameters, with one of an appropriate size selected for each type of garment produced. Special machines of small diameters are used for tights, stockings and socks, while larger machines produce tubes of fabric for cut and sew work.
This Scott & Williams circular machine was manufactured under licence by Blackburn and Sons of Nottingham. (Leicester City Museums Service, T.7.1926.0.0)
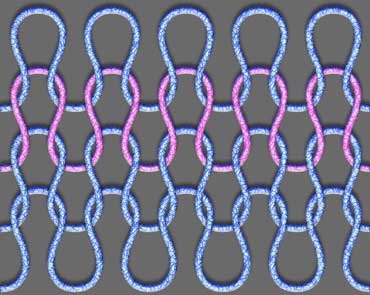
Course
The term 'course' in knitting refers to a horizontal row of loops. On a Lee-type frame a new course was created on each cycle of the thread being laid and sinkers moved. In hand knitting a course is completed when the fabric has been transferred from one needle to another.
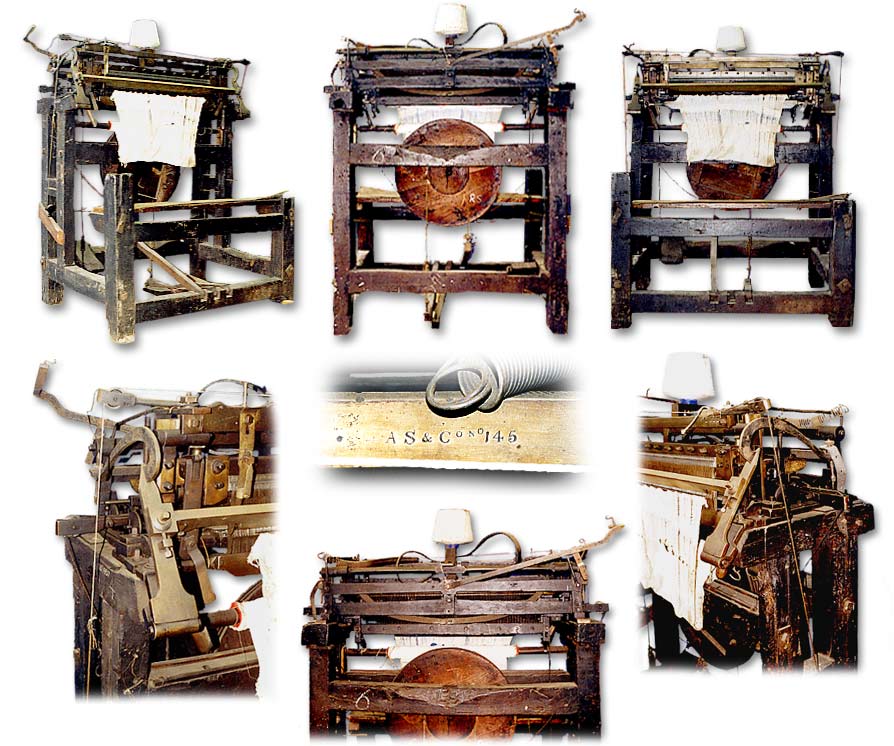
Machine used to mske single piece fabric for cut-ups.
Cut and Sew (Cut Ups)
From the late eighteenth century the introduction of wide frames enabled greater widths of fabric to be produced. Framework knitters soon realised that it was quicker for them to cut the shape of a garment out of a wide piece of fabric than to spend time shaping the fabric on the frame. This method was the precursor of the modern and technically advanced 'cut and sew' industry.
Cutting into knitted fabric broke the mesh of continuous loops and the edges unravelled if they were not carefully oversewn. Garment seams in cut and sew work were more bulky than selvedge seams as they not only had to hold the fabric pieces together, but they also had to stop the separate pieces from fraying. At that time fully-fashioned garments had a finer finish and were seen as superior to 'cut ups'.
From the mid-nineteenth century, steam-powered circular machines quickly produced broad tubes of fabric for cut and sew work. Complex machines were introduced that could produce patterns and shapes that could not be equalled by fully-fashioned technology. Large numbers of women were employed at banks of sewing machines to assemble the various garments produced. Singer, the sewing machine manufacturer, introduced 'The Singer Handbook for the Hosiery Trade' to provide manufacturers with a guide to how long different sewing tasks should take and which Singer machine they should use for the task.
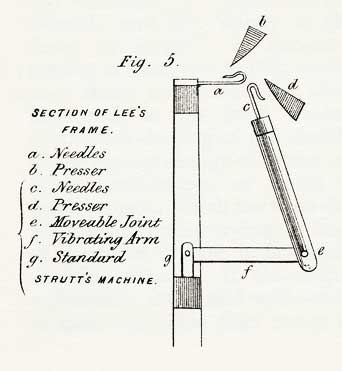
Derby Rib Frame
Jedediah Strutt patented the Derby rib frame in 1758. Strutt discovered that by reversing the face of alternate columns (wales) of loops, a more flexible and elastic fabric was created. The reversing process was achieved by adding to the Lee frame a vertical bed of needles that interlocked with the horizontal bed. The width of rib required determined how many needles were worked from each bed. Knitting on alternate beds (one horizontal needle to one vertical needle) created a fine thin rib while a broad rib was produced by knitting on a greater number of needles before alternating to the other bed (e.g. three horizontal needles to three vertical needles).
The elasticity of ribbed fabric has made it popular for parts of close-fitting garments that need to stretch. Sock tops and collars and cuffs on jumpers commonly use ribbed fabrics.
Strutt's rib attachment added a second bed of needles to Lee's frame. The attachment knitted alternate loops within a course on the opposite bed.
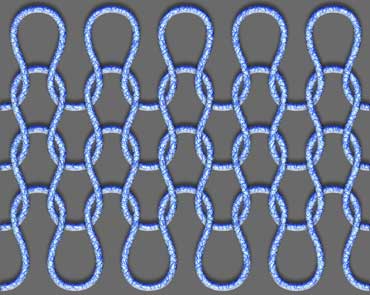
Face
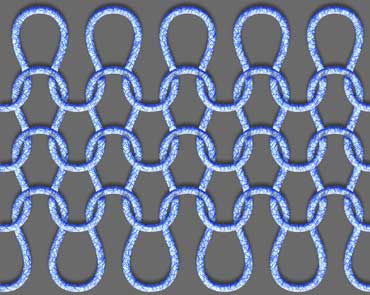
Reverse
Face and Reverse
The face of a loop is the side to which the loop is pulled through. The reverse or back is the side from which the loop is pulled. The loops of a plain fabric all face the same direction, while in a simple ribbed fabric the wales alternate in direction.
The face of a loop is the side to which the loop is pulled through.
The reverse or back of a piece of fabric is the side from which the loop is pulled.
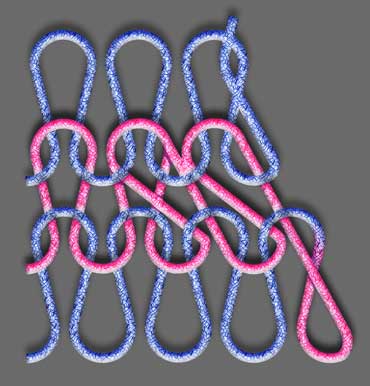
Narrowing
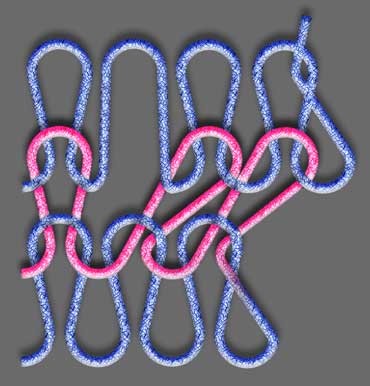
Widening
Fashioning Marks
Fashioning marks occur on fully-fashioned garments where loops have been transferred sideways to either narrow or widen a piece of fabric. The mark appears as a break in the regular loop structure of the fabric.
Moving the outer loops at the selvedge inwards narrows fabric. Usually two or three loops will each be transferred across to the next needle in. The innermost loop is moved to a needle already occupied by a loop, causing two wales to combine. The reverse transfer widens fabric and creates a small hole at the innermost loop. Subsequent courses have an additional wale.
Narrowing fashioning mark
Where loops are moved inwards to narrow a piece of fabric a fashioning mark is created. This is caused by the innermost transferred loop being placed onto a needle already occupied by a loop. A slightly thicker fabric is created at this point.
Widening fashioning mark
Where loops are moved outwards to widen a piece of fabric a fashioning mark is created. A small gap is created in the fabric where a needle is unused for one course after the loop has been transferred sideways from it.
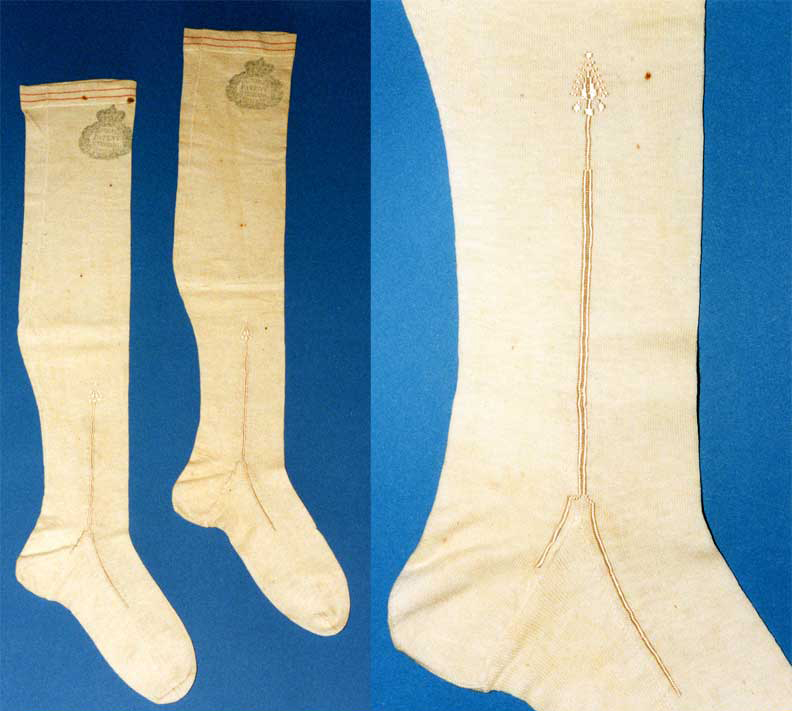
Fully fashioned stockings
Fully-Fashioned
Fully-fashioned is a term used in the industry to describe the production from Lee-type frames and its successors such as Cotton's Patent and Reading machines all of which used bearded needles. The width of a fabric is increased or decreased by changing the number of needles used in the knitting process. Where a change in width is required, a few outer loops are moved inwards or outwards to achieve the width change. This process creates fashioning marks on the fabric. The fully-fashioned method was considered superior to the 'cut up' work during the framework knitting period and for sometime since. Although fully-fashioned knitting is slower and more expensive to knit, it produces less waste than cut and sew work.
In the early days of the industry the garment panels were assembled by hand stitching but in modern times the favoured method has been cup seaming.
A variation on fully-fashioned – hand powered V bed flat machine with shaping capacity have been developed. These use latch needles and are sometimes used for the production of heavy garments such as fishermens' jumpers. These machines are a somewhat similar to a domestic knitting machine but are much more sophisticated. The whole situation is now somewhat blurred as the most advanced flat machines now have all the advantages of cut and sew machines and can produce shaped panels.
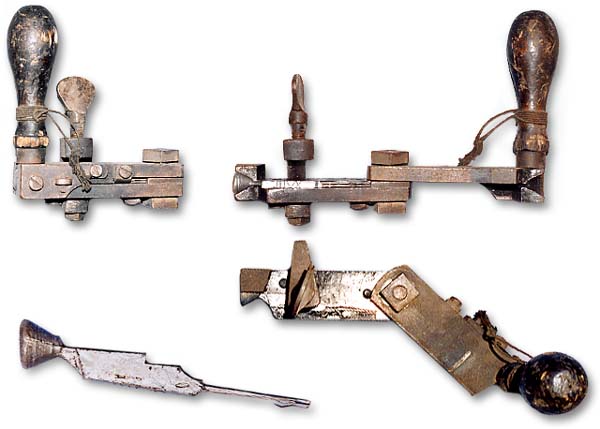
Needle mould
Gauge
The gauge of a frame or machine determines how fine a fabric it is able to produce. Widely spaced needles produce large loops and a coarse fabric, usually from a thick yarn. In the modern industry nylon and Lycra yarns are often used with fine gauge machines that use tightly packed small needles to knit a fine loop mesh.
The gauge for Lee stocking frames was calculated on the basis of how many leads were held in the bed per three inches. The shank of a needle was placed into molten lead held in a mould. Once removed from the mould, the lead was then placed into the frame to hold the needle in place. Sometimes two or three needles were placed in one lead and, therefore, a three needle lead had more needles in a given gauge than a one needle lead.
Circular knitting machine gauges are calculated by dividing the number of needles by the circumference in inches. This gives a figure for the number of needles per inch.
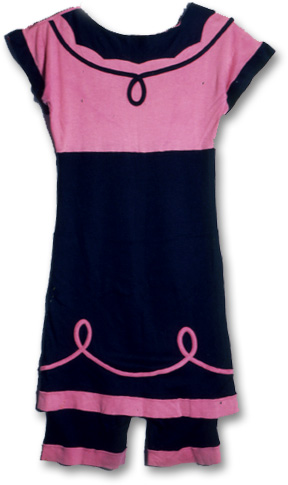
Interlocked garment
Interlock
Scott and Williams of the USA patented the interlock process in 1908. The process uses two threads to knit a fabric that is faced on both sides. Each thread knits a ribbed fabric and the double face is achieved by the two threads crossing over between wales, consequently the face of the rib from one thread hides the reverse of the rib from the other thread.
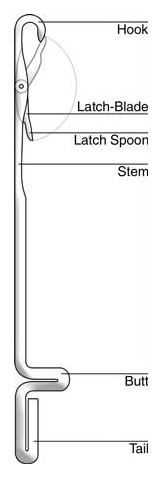
Latch Needle
Matthew Townsend, a Leicester hosier, patented the latch needle in 1849. Townsend spent much of his time developing new knitted fabrics and he investigated a simpler way of knitting purl fabrics. Purl fabrics required two beds of bearded needles and pressers to alternate the face of loops between courses. A double-headed latch needle was developed as a result of the research to allow the alternation to be achieved on one bed of needles. A single-headed latch needle was also developed to provide an alternative to the bearded needle.
The needle consists of six main parts:
- Stem – Used to hold the course of old loops
- Hook – The hook is used to catch a thread and form loops.
- Rivet – Holds the latch in place and allows it to pivot.
- Latch – The latch combines the task performed by the presser bar and the beard of the bearded needle.
- Butt – The butt enables the movement of the needle to be controlled by a cam mechanism. A track raises and lowers the needle.
- Tail – Used to provide support to the needle.
The latch needle knitting cycle starts with the old loop trapped inside a closed latch. The needle is pushed up and the old loop slides down the stem, opening the latch in the process. A thread is then laid in front of the stem between the rivet and the hook. As the needle is pulled down the hook catches the thread and forms a new loop. The old loop now slides back up the stem, closes the latch and falls off the end of the needle. The cycle is then repeated.
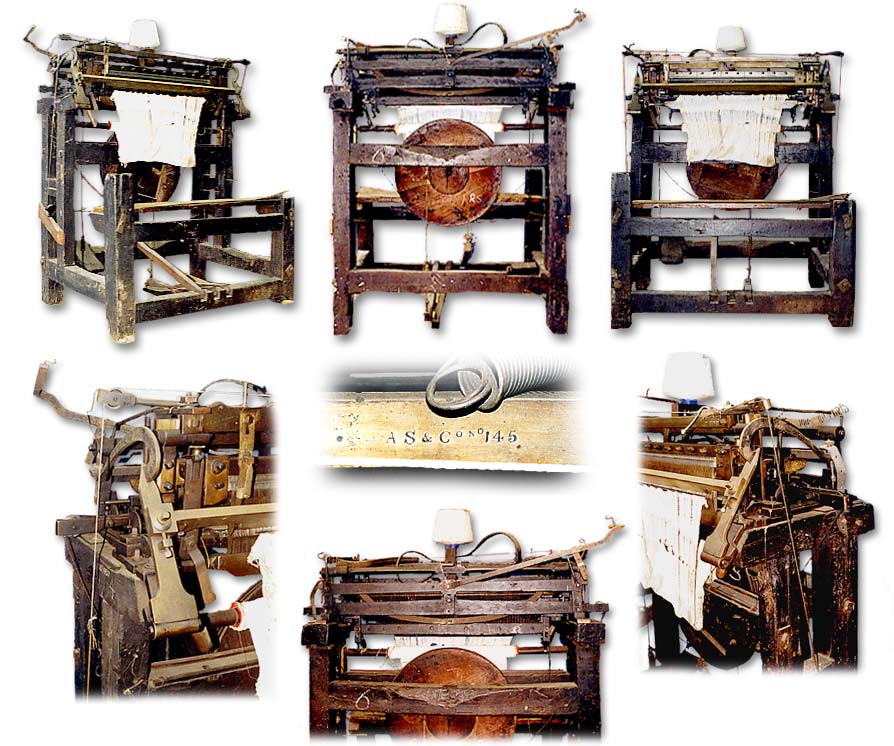
Lee's Knitting Frame
Lee's frame brought together a number of components to create a machine capable of replicating the movements of a hand knitter. A wooden frame provided a seat for the framework knitter and pedals to control the knitting bed. The knitting bed was bolted onto the frame and could be removed for maintenance. The ability to change the bed has meant that surviving frames do not necessarily have their original knitting beds.
The knitting process started with the framework knitter laying a thread across a horizontal row of bearded needles. Jack sinkers were placed between the needles and allowed to fall one at a time onto the yarn to form loops. The jack sinkers were hung from pivoted levers known as jacks. Springs locked onto the back end of the jacks and held them in place until a metal block (known as a slurcock) was pulled along a carriage to knock the springs back and release the jacks. Two pedals pulled the slurcock from side to side. Once the sinkers had dropped they were used to bring the partially formed loops forward and under the hooks (beards) of the bearded needles. A metal presser bar was brought down by a further pedal to press on and close the beards and trap the new course of loops. The sinkers were then used to bring the old course of loops over the closed beards. A locker bar then pushed the jacks back under the springs to lock them in place ready for a new thread to be laid.
After Lee's death, his brother improved the frame by adding a row of fixed sinkers. Fixed sinkers were placed between each jack sinker and were brought down all at the same time after the jack sinkers had fallen. The fixed sinkers allowed needles to be placed closer together and a finer gauge fabric to be produced.
Lee's first frame greatly increased the speed of the knitting process and produced around 600 loops per minutes compared with a hand-knitter’s 100 loops per minute. Improved versions of the frame used for knitting silk stockings formed 1000 loops per minute.
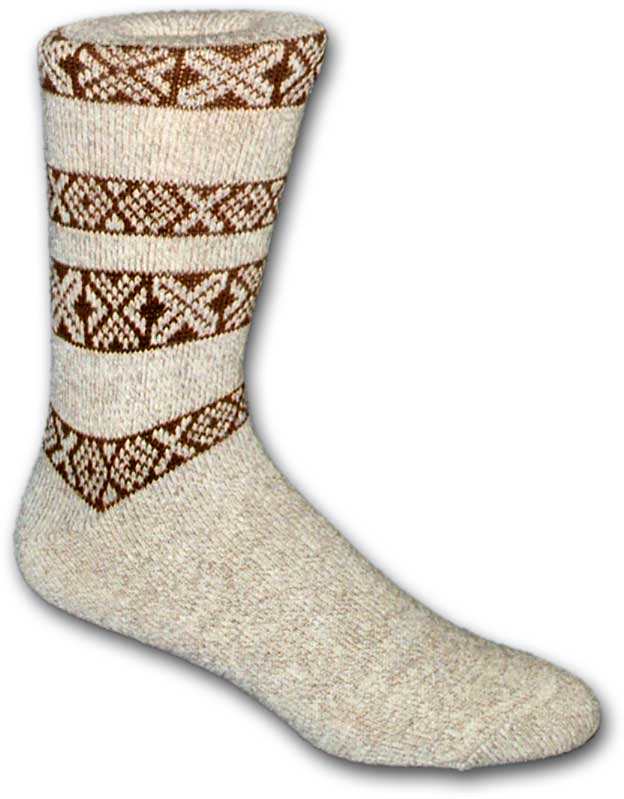
Modern sock with closed toe
Linking
The linking process is frequently used for attaching collars to fully-fashioned and cut and sew knitwear.
In the case of linked socks, a tube of fabric is brought from a knitting machine and the final course of loops at the toe end is placed onto a row of points. The toe is then joined together by sewing a thread through the loops. The seam becomes part of the knitted fabric and a high quality flat seam is achieved suitable for top of the range socks.
When overlocking was used to close sock toes this created a slight ridge. The modern methods of toe closing available from the early 1970s use special machines and in further developments the latest technology produces socks that are closed by the knitting machine.
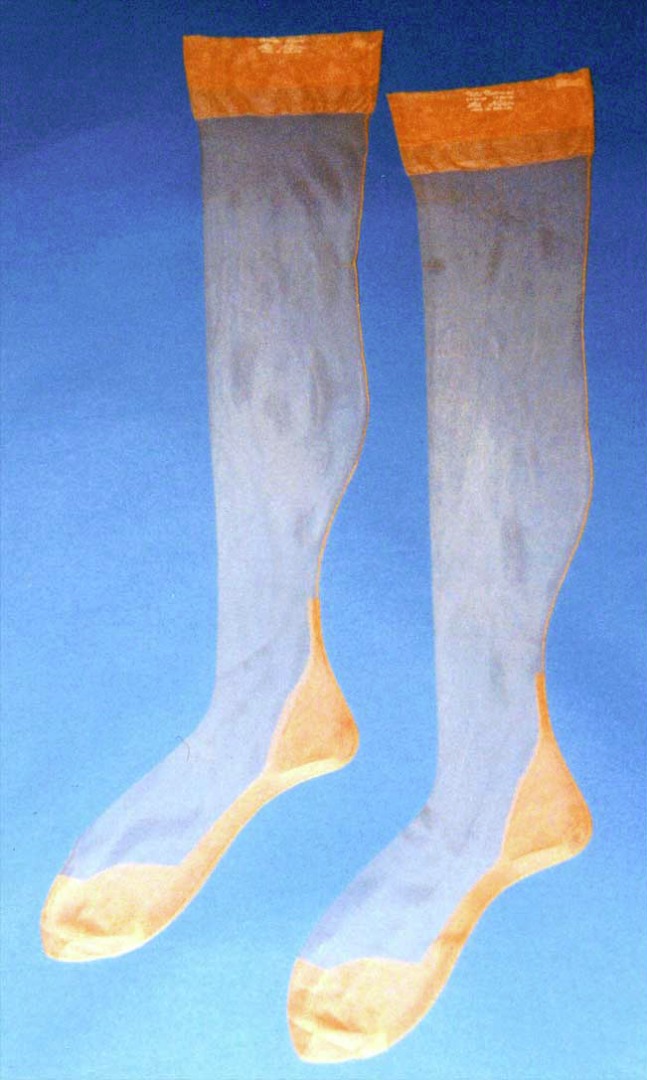
1960s stockings with mock-seams
Mock Seams
Fully-fashioned stockings remained the most desirable stocking up to the introduction of nylon after the Second World War. One distinguishing feature of the fully-fashioned stocking was the seam that ran up the back of the leg. Cheaper seamless stockings knitted on circular machines did not have the seam mark. To imitate the more expensive fully-fashioned stockings mock seams were created by bunching a few wales together and sewing round them. In some cases mock fashioning marks were also knitted into a stocking. Stockings with mock seams cost a little more than plain seamless stockings.